Manufacturer’s guide to specifying a conveyor oven
If you manage a specialized manufacturing process or build a product that meets strict requirements, you can’t rely on a standard conveyor oven. You need something customized to your process.
Customization calls for detailed specification. Engineers sourcing conveyor ovens need to provide oven manufacturers with insight into their upstream and downstream manufacturing processes, on top of info about their product and thermal process.
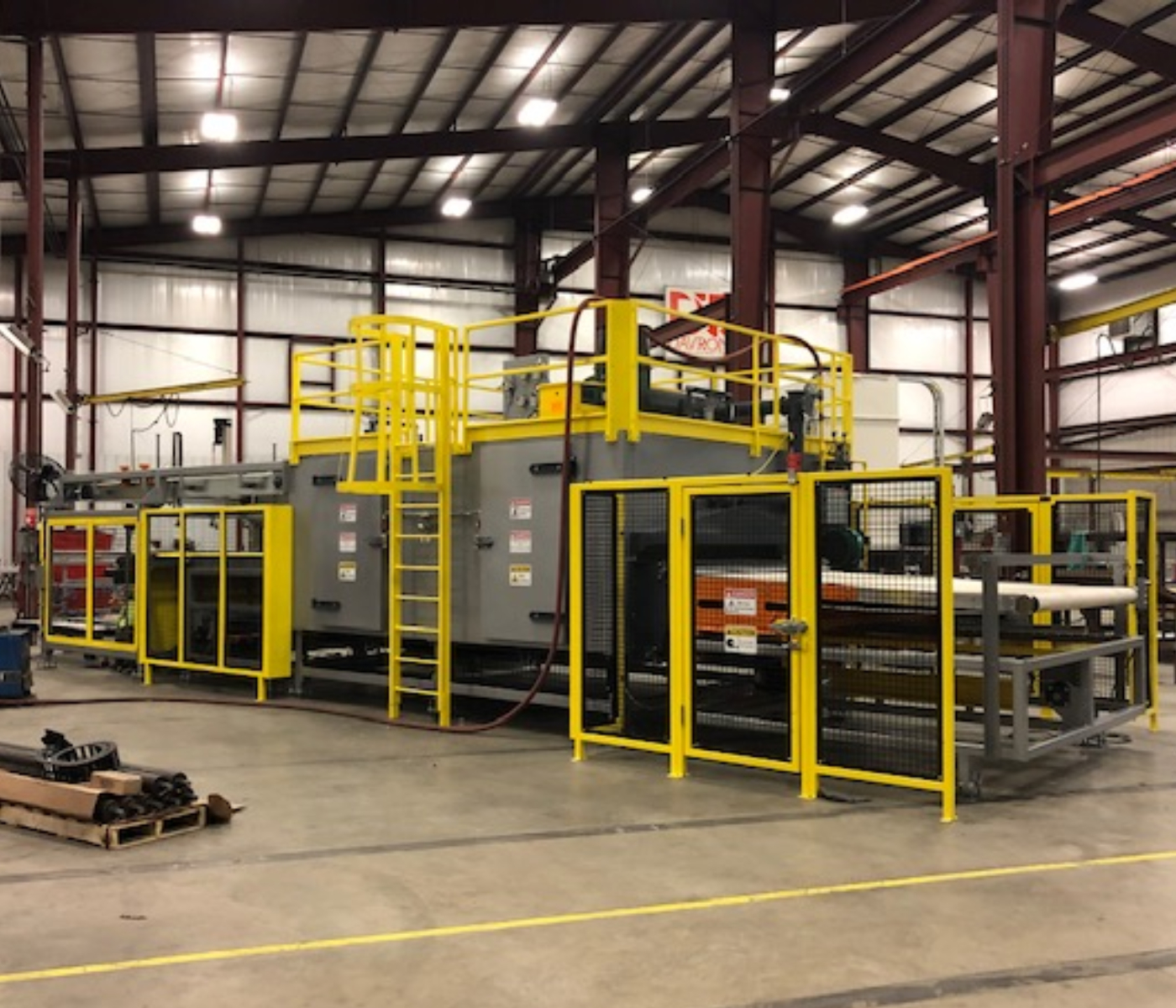
This specification work determines the success or failure of equipment you’ll rely on for years. Getting the details right is crucial, but not every manufacturer has a thermal processing expert to turn rough requirements into detailed specs.
This guide covers the information your oven manufacturer will use to design and build the perfect conveyor oven for your product and process. Read through for an understanding of why each detail is important, or get in touch to set up a consultation with a Davron engineer.
Oven type: continuous or indexing?
There are many ways to get your product through an industrial oven. All of them fall under one of two categories: continuous or indexing. Which is best suited to your application depends on your upstream and downstream manufacturing processes.
Rule of thumb:
Use an indexing oven if your process requires staging of parts, especially if they’re staged in groups. Use a continuous oven if you produce a large volume of similar parts in-line.
Continuous conveyor ovens move product through them at a steady rate. If you have a continuous upstream process, we can design an oven to accept parts directly from almost any upstream process without requiring additional labor.
Indexing conveyor ovens move the product in a stop-and-go sequence. They convey, then stop, then convey again, ad infinitum. They are useful when upstream or downstream processes are indexing or parts are processed in batches.
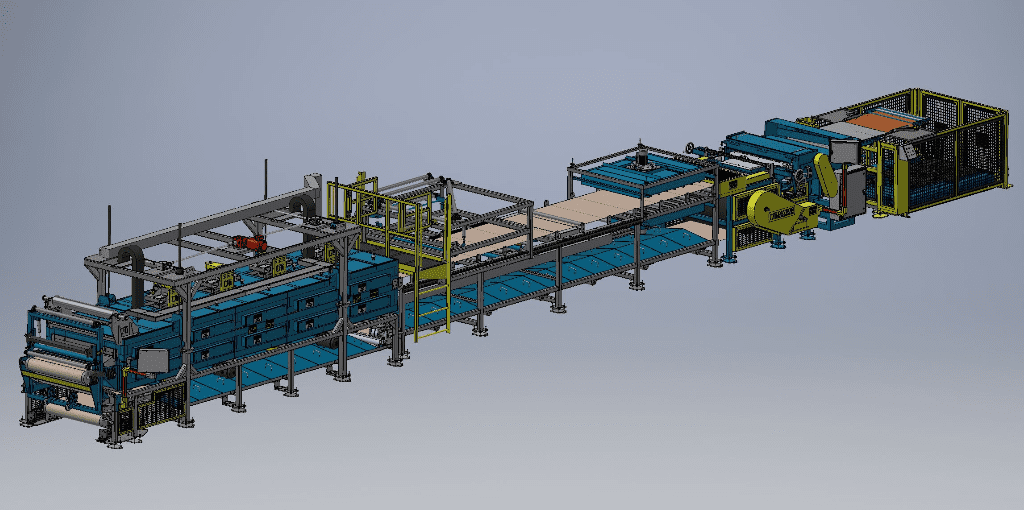
If your upstream processes produce parts in batches of four, you can load all four parts into an indexing conveyor oven simultaneously. But making this process sing requires your downstream process to accept four parts at a time.
Some engineers prefer indexing ovens when they desire strict control over heating and cooling sequences within the same oven. We can build doors between different oven sections that open for parts to pass through and close behind them, to limit the amount of heat from one section of the oven that bleeds into the next.
But there are ways to achieve similar levels of control with continuous ovens. We build walls between sections with just enough space for product to move through them. If product is continuously moving from chamber to chamber, that space is mostly filled, and the amount of heat-loss is limited.
3 questions you should ask yourself
- Am I processing large quantities of similar products?
- Are my products staged individually or in groups?
- Does my upstream or downstream process offer any material handling challenges?
Conveying system
Whether you need a continuous or indexing conveyor oven comes down to your ideal manufacturing process. But the type of conveyor you use and its arrangement in your oven will depend on your product and your facility environment.
Oven configuration
Ovens can be arranged horizontally, vertically, at an incline or at a decline, with a single pass through the oven chamber, a serpentine pass or — in extreme cases — in a spiral. Each arrangement has distinct pros and cons.
Most conveyor ovens are horizontal. But vertical ovens appeal to manufacturers with limited floor space looking for high processing capacity out of the smallest possible footprint. Rather than pass a part horizontally across your plant, you can pass it straight up or down, drastically reducing the floor space needed for operation.
Bulky parts are a poor fit for tight turns and, therefore, don’t do well in vertical ovens. But compact parts like pistons can sit in trays that take tight turns at the top or bottom of a vertical oven, like in this example.
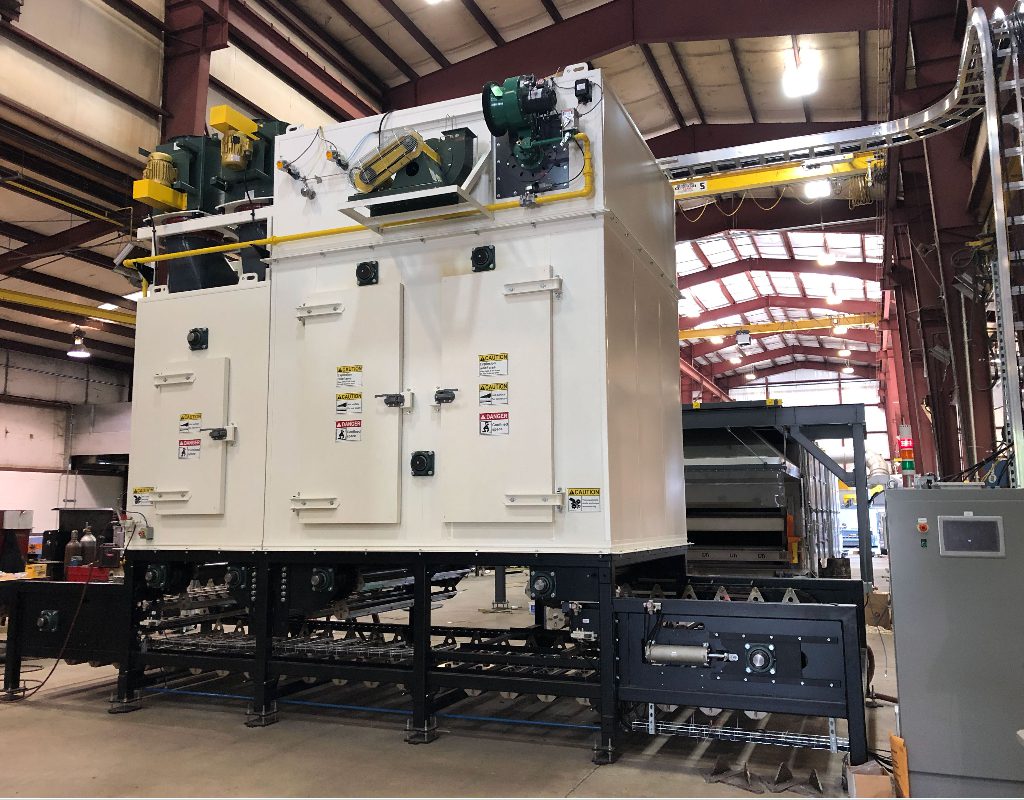
The only reason we’ve ever built an incline or decline oven was because the customer needed their parts to start thermal processing on one level of their plant and end on another. But we’ve used incline and decline conveying in horizontal oven arrangements to merge parts for forming after pre-heating.
Spiral ovens have some distinct benefits but some serious drawbacks as well. We built this spiral oven to continuously cure small silicone parts for a medical device manufacturer. And we advised them to find another way — one that didn’t rely on a spiral conveyor.
Why?
The friction drive system constantly wears, everywhere. They use either metal on metal contact or metal on plastic contact (in which case you’re temperature limited). We see it as a guaranteed maintenance item, where the parts experiencing the most wear are difficult to access in the center of the belt.
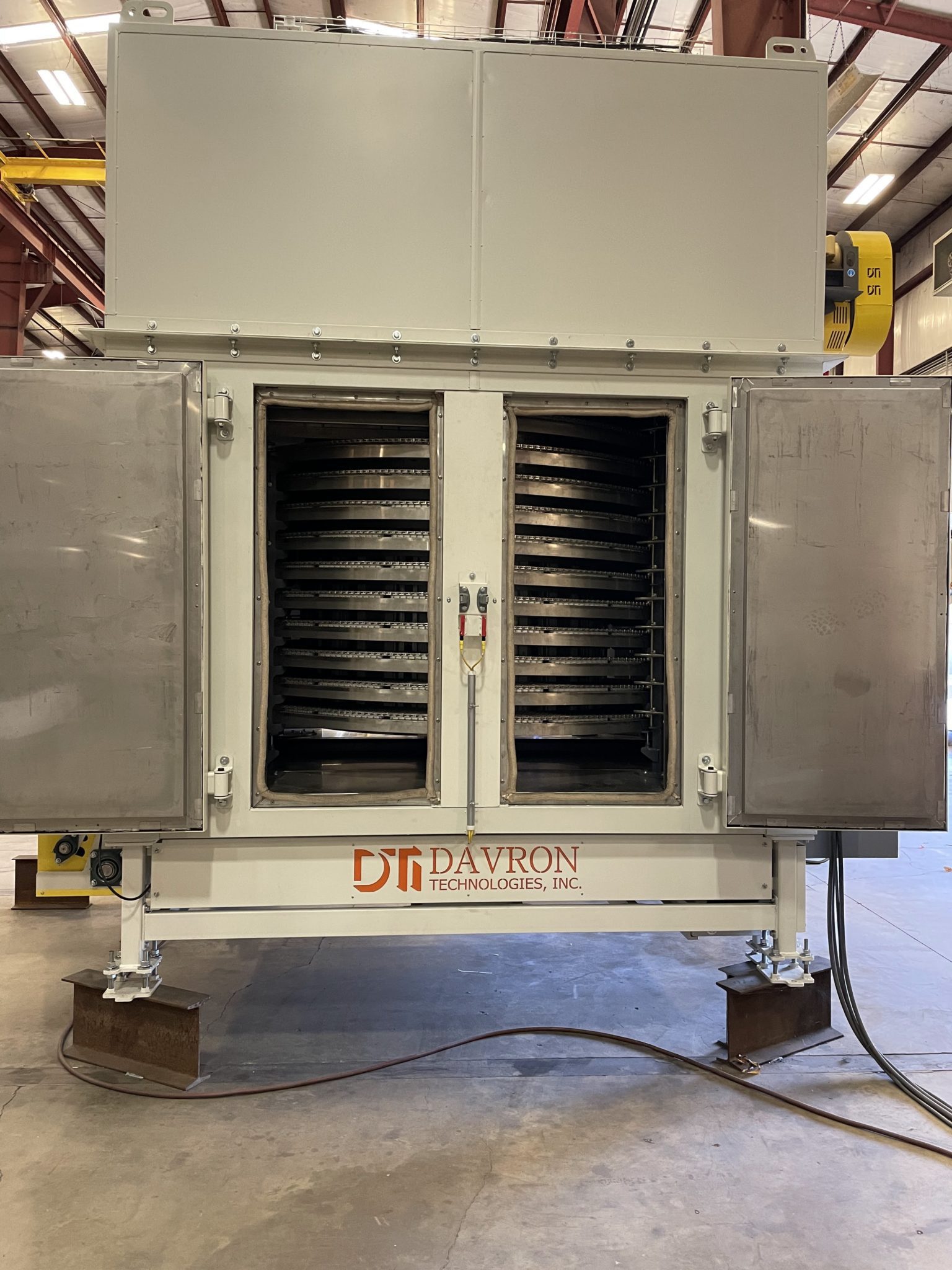
But the customer was adamant, and they love the oven because it offers an extremely high product density. There’s over 300 feet of belt in the oven, which has a 15 ft. by 15 ft. footprint.
Single pass ovens are common because their simplicity makes operation and maintenance easy. Serpentine ovens convey parts one direction and then turn them 180 degrees, as many times as needed. Every turn the conveyor makes leads to a wider oven, so available footprint can become an issue.
The simplicity of a straight conveyor is a huge selling point for a single pass oven, in that they’re cheaper to build and maintain, but there are some circumstances in which serpentine configurations make sense.
One is in vertical ovens. Conveying a part up and then turning to come back down proves much simpler and more efficient than making a horizontal turn. And you’re still saving floor space with a vertical oven.
On a horizontal oven, we prefer to stack the oven chambers vertically and make a similar turn: Parts convey through the top chamber, drop down to the bottom chamber and pass back, getting two passes without need for extra floor space or a horizontal turn.
Conveyor details
Which conveying system makes the most sense for your oven will depend on your product. Your first decision is your conveyor type, from the following:
- Belt
- Chain
- Rollers
- Monorail
Belt conveyors are the simplest, cheapest option in most cases. They can be designed to carry your part’s unique tray or with a material well-suited to carry your part. Some options are:
- Flat wire
- Wire mesh
- Rubber
- Teflon
- Plastic
- Solid
- Flighted
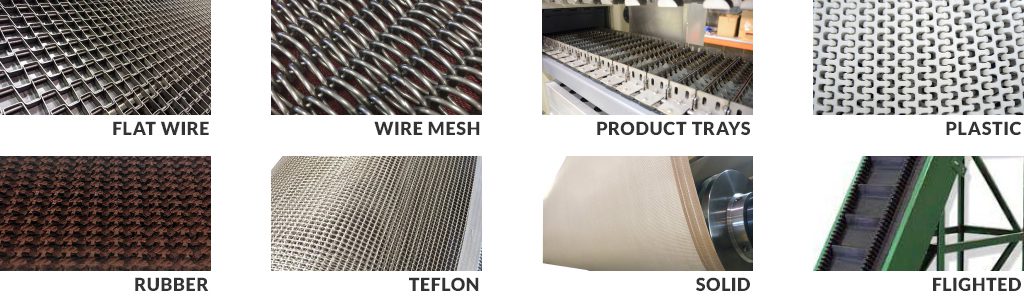
Chain conveyors are used when manufacturers move parts through their process on carts and want to move the entire cart through their thermal process as well. They can be designed to carry specific carts when needed.
Rollers typically lay flat and parallel. In thermal processing applications, they are metal but can be coated for more desirable contact with your part or its tray. Horizontal conveying systems that need to turn generally rely on rollers, since the conveyor channel doesn’t require a constant width in a roller system.
Rule of thumb:
Applications where rollers make the most sense are those with heavy products that would create too much friction in a belt conveyor system, leading to excess wear.
In overhead monorail conveying systems, parts are carried from a rail system in the top of the oven chamber. It’s perfect for long, skinny parts. When part length becomes part height, more parts fit into the oven at once, and it becomes easier to heat them evenly.
Monorail systems can turn more simply, so when the parts are skinny, they can make multiple passes in the same heated chamber, like in this oven used to heat automotive instrument panels.
3 questions you should ask yourself
- What is my desired conveying speed?
- What oven size and shape would best fit my plant?
- Does my product require custom trays or tooling?
Heat source: Gas or electric? Convection or infrared?
Your heat source is something an oven manufacturer will want determined early in the oven design process. Often, for convection ovens, natural gas makes more sense from an operating cost perspective. It’s typically a lot cheaper to run than electric.
Rule of thumb:
If your product has a large thermal load, natural gas will almost certainly prove the most efficient heat source for your application.
We’ve had customers ask for natural gas infrared (IR) ovens from us, but they would have been incredibly expensive, both up front and in perpetuity, so we proved viability of a natural gas convection oven system for their product.
IR ovens do have their place, though, for certain applications. They work like a toaster, in that heat cooks the outside of the part without penetrating the part well. Sometimes that is ideal.
We frequently use IR to heat carpet backings that have heat-activated glue on top. The customer would prefer if the carpet face didn’t heat up, since it would leave an imprint on the conveyor belt if it did. All they want is for the glue to get hot, so IR heat from above is the perfect solution.
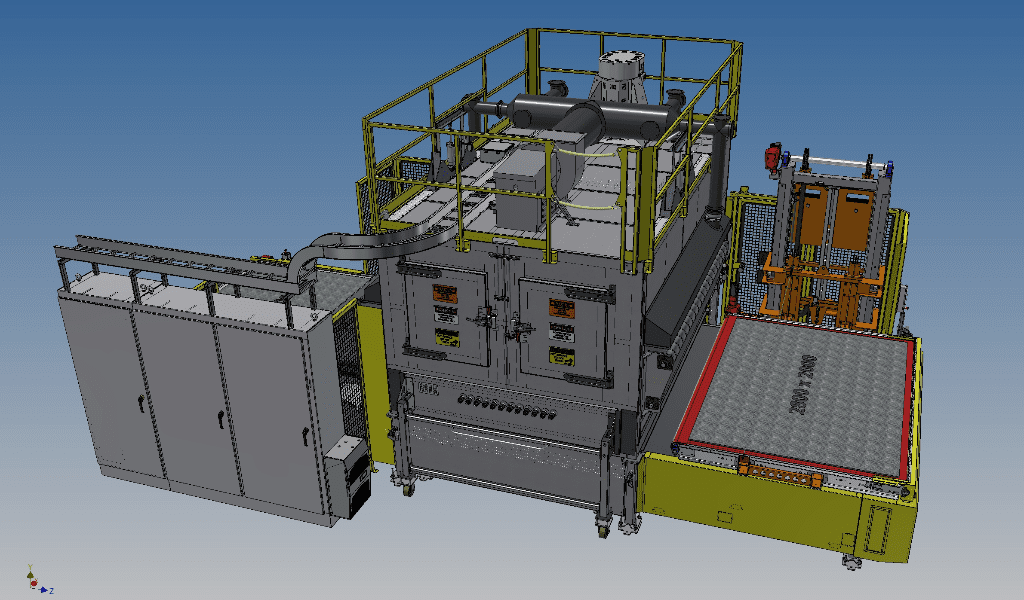
An interesting example that uses both convection and IR heat
In this bi-level oven system, the operator loads a top part and a bottom part into different ovens from the same spot. The parts are indexed through different heating processes. A lightweight backing material moves through the convection-style top oven for pre-heating, and an automotive carpet layer with adhesive moves through the IR bottom oven to activate the glue.
Then, a decline conveyor merges the two parts precisely on top of each other before it enters the next stage of production as a fully assembled part.
3 questions you should ask yourself
- What are my local utility rates?
- What power source is my plant equipped to handle today?
- How much product weight will be processed per hour/shift/day?
Temperature requirements and heating profiles
The three main things we want to determine when designing a custom oven are your desired operating temperature, your maximum operating temperature and the thermal load of your part (the amount of energy it takes to heat that part up).
If you’re heating up engine components by putting room temperature heavy metals into a hot oven, you’re introducing a high thermal load. There’s a lot of energy required to bring that product up to temperature.
We can help determine the thermal load of your part based on some of its specs (material, weight, etc.) via understanding its specific heat and doing some math.
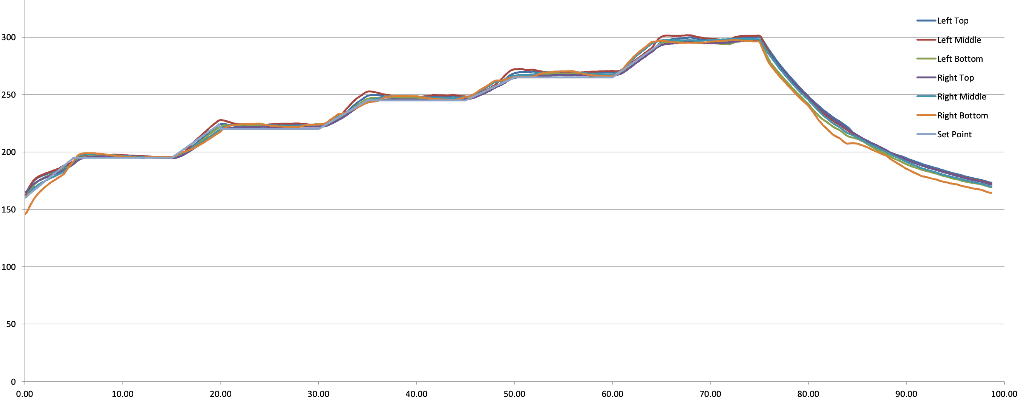
Heating and cooling profile
Precision thermal processing goes beyond setting an oven temp and waiting for a result, and different parts require very different treatment from ovens. Some parts need time to ramp up to temperature based on their storage temperature
Some parts need time to soak after reaching temperature. And that only accounts for heating. Cooling is an important factor too. If operators are handling parts immediately after thermal processing, you likely need an oven that can help cool a product back down to a safe temperature.
3 questions you should ask yourself
- Should I specify higher temperature capacities to account for future products?
- Does my product need to ramp to temperature or soak for any amount of time?
- What temperature is considered cool enough for my process?
Airflow arrangement
If you’re looking for a custom-designed oven, you’ll achieve extremely precise airflow control. If you’re working with Davron on an oven, we’ll be able to blow air on to the part from any single direction, or from any two directions in a profile view of wherever parts are traveling.
When traveling a part horizontally, top-to-bottom and/or bottom-to-top airflow typically makes the most sense because it allows you to heat the entire part evenly. If your part is traveling north to south, and all your hot air is blown on the part from east to west, the part will heat unevenly. But vertically oriented airflow can guarantee even heating of the part.
If the part is vertically oriented, though, horizontal airflow can offer more even heating. So the type of product you’re processing and the method you’re using to convey it play a big role in determining the best airflow arrangement for your process.
If your product is lightweight, you’ll also want to consider whether certain airflow may blow your product around in the oven chamber.
3 questions you should ask yourself
- What shapes am I processing?
- Where does hot air need to be impinged on the product?
- How heavy are my products?
The importance of your product, your plant and your process
The examples in this guide are of other companies’ best-fit ovens. Yours probably isn’t here. But consideration of all the relevant details about your product, facility and process can help you identify what your best-fit oven looks like.
Remember to think about your upstream and downstream processes and equipment. A best-fit oven will integrate with your entire process smoothly.
Let’s collaborate on your ideal oven
Not everyone knows every spec they need their oven to meet, so don’t worry if you don’t have all the details nailed down. Plenty of our customers come to us with a product, a goal temperature, and a process problem they need to solve. You can rely on our expertise to turn a napkin sketch into a quote-ready design.
If you’re interested in working on specifying or building a custom oven, reach out. We can make sure you’re talking to an expert as quickly as possible. Just let us know what you’ve got so far, and what you’re hoping to achieve.