When should you upgrade your industrial oven?
Nobody wants to get caught in dire need of a replacement oven to resume production.
Thankfully, industrial ovens don’t die often. Regular maintenance is usually enough to keep an oven working. When they do fail, they tend to fail gradually, giving you time to line up a replacement.
But the most successful manufacturers don’t think about new ovens as replacements. They think about them as upgrades. And watching downtime put your facility in the red isn’t the only way to understand when an upgrade could drive value.
In this piece we’ll talk through how to recognize the signs that it’s time for a new oven — and why not every replacement is a true upgrade.
Performance-related signs that you should upgrade
You should upgrade your oven if it isn’t reaching and maintaining the required temperature or providing consistent airflow to heat your product reliably. Manufacturers typically install an oven that can promise better performance ASAP.
But there are issues we see manufacturers work around when a new oven would be the most sensible solution.
If your oven struggles with maintaining temperature while running for long periods of time, an upgrade would drive huge ROI by allowing for consistent production continuously. Some manufacturers combat over or underheating by shutting their ovens off every six hours. But what does that downtime cost?
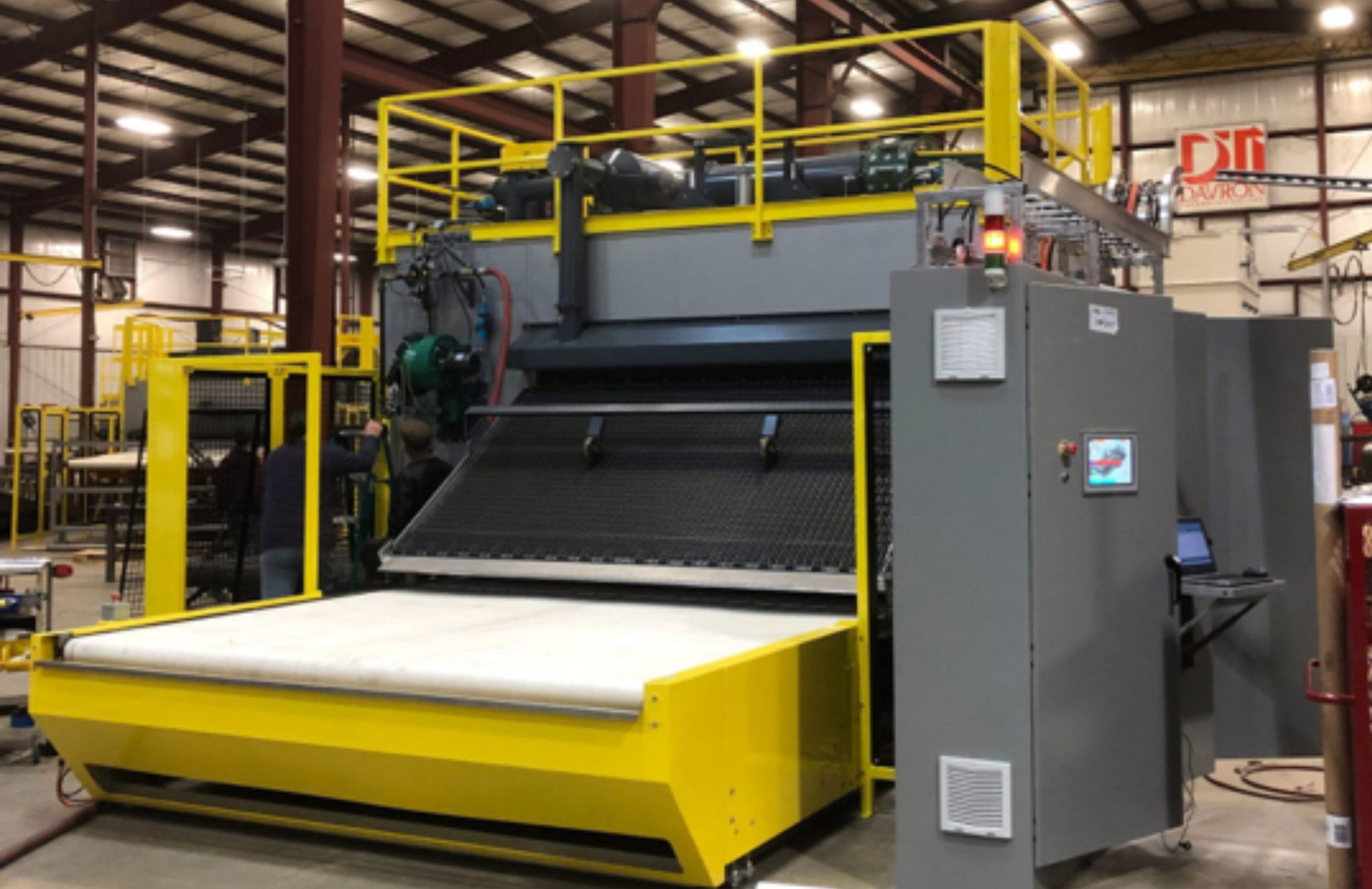
When your TV goes out, you may get up on the roof and fiddle with the satellite or reset your router to try and get The Office back up and running as quickly (and with as little effort) as possible. But power cycling industrial equipment during production is like slapping a band-aid on a bullet wound. Solving your temperature maintenance problem for the long-term would be a huge success for your company.
Some manufacturers use ovens that aren’t ideal fits for their needs. That’s when you see manufacturing practices like running ovens with the doors open to keep the internal temperature from climbing too high for their process. Aside from creating a hot work environment for employees, this wastes tons of energy and indicates that a right-fit oven upgrade would pay for itself quickly.
Process-related signs that you should upgrade
Even if your oven itself performs well, there could be process-related signals that upgrading is a smart move. Often, manufacturers aren’t aware of the ways an oven can drive plant-wide process improvement or hold back production efficiency.
Consider the value of an upgrade if your current oven:
- Uses an outdated human-machine interface (HMI) or programmable logic controller (PLC)
- Uses a batch process where a continuous process would offer more value
- Lacks standardized operation or maintenance processes
- Is comprised of parts without a reliable replacement market
Why up-to-date oven programming and interface matters
Plenty of old ovens work well, and the simple fact of an oven’s age doesn’t dictate the value of an upgrade. But it’s worth evaluating whether your oven is simple to operate and contributes intuitively to your process.
Almost every oven has a PLC guiding and monitoring its operations beneath the surface. But today’s PLC’s perform functions that ovens of the past only dreamed of. How detailed is your oven’s self-monitoring? Does it report on its own performance?
We’ve worked with manufacturers who were recording oven operating data by hand in order to produce robust quality assurance records. An upgraded oven with the right HMI can record and store that data automatically in whatever format you need, so you can access it wherever you need it.
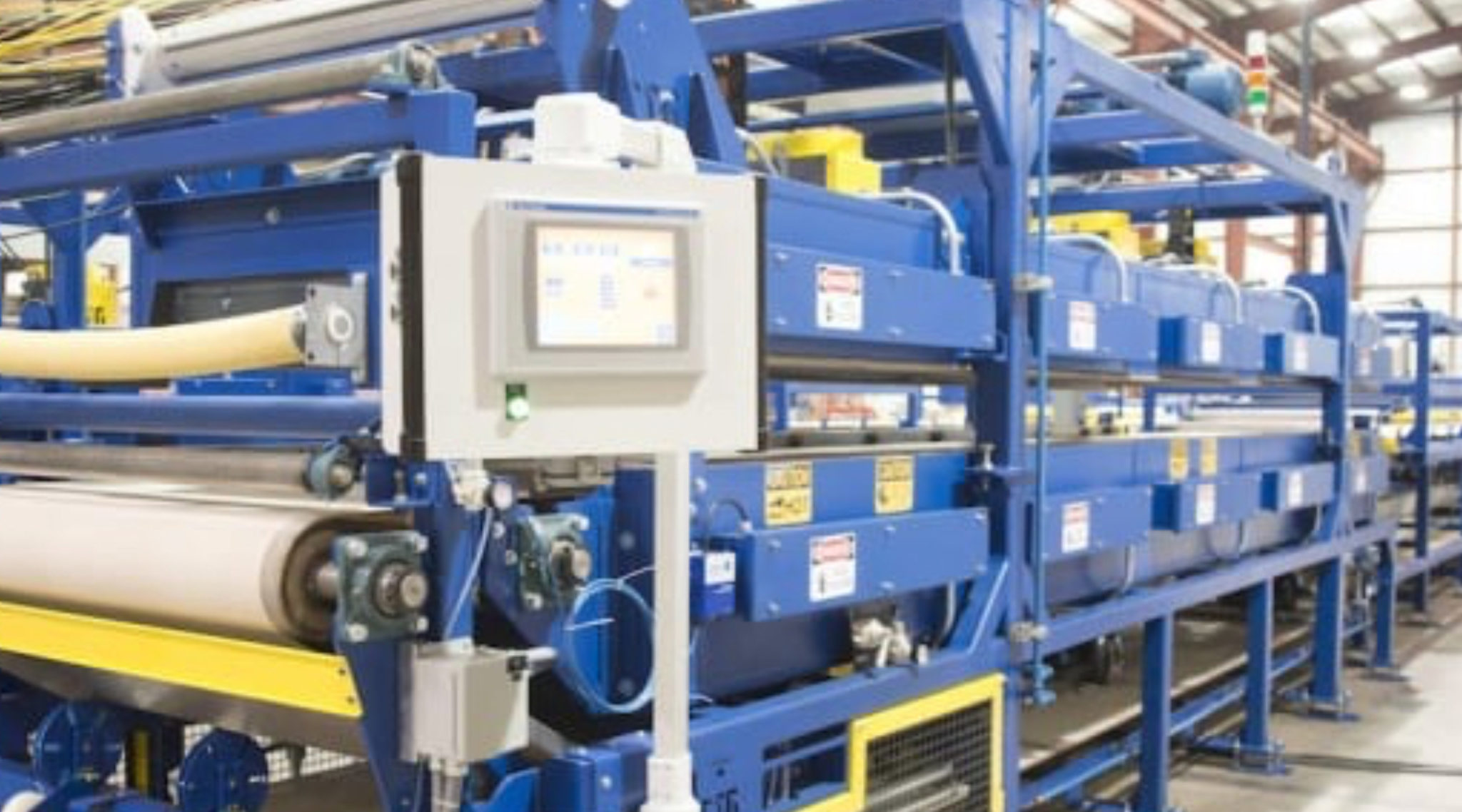
Maybe your process isn’t held back by an oven without smart data recording or an intuitive HMI. But your oven shouldn’t need a stenographer just because you’re in a heavily regulated industry or work with frequent equipment audits.
And with the right PLC, your oven can help you with more than thermal processing. A PLC that catalogs the right kind of operation, in tandem with an easy-to-use HMI, can equip maintenance teams with real-time information on oven performance and detailed breakdowns of any alarms. It’s worth evaluating how much time and stress could be saved with an equipment upgrade.
How a batch oven could be holding you back
If you are using a batch oven to process a high volume of similar parts, you need to consider upgrading to a conveyor oven. Here’s why:
Batch ovens require labor and time to load and unload, and their throughput is limited by design — you load the number of parts that fit and run the oven through its process cycle. When the process is complete, you remove the parts.
Say it takes one minute to load six identical parts into your batch oven and one minute to unload them. And your processing time is five and a half minutes, including time for the oven to cool down. That means six parts are processed in seven minutes and thirty seconds.
A conveyor oven processes parts continuously. Parts can enter and exit the oven at any throughput, provided you have space in your facility.
Those same six parts as above could enter a conveyor oven one at a time every ten seconds and exit at the same rate. One minute to load and one minute to unload, just as before. Let’s assume the same processing time to show the impact a process-oriented change can have.
What’s the difference? Your hypothetical batch oven only processed those six parts in the given timeframe. But a conveyor oven is continuously accepting new parts. If you do the math, the hypothetical conveyor oven (with identical processing time and loading/unloading time) worked on a total of 45 parts during that same timeframe. A completed part will exit the oven every ten seconds, no labor required.
The impact of non-standardized processes on operation and maintenance
Evaluate your oven operating process. Is it documented, or did you need to ask an operator to show you? Or are you one of those operators who knows the undocumented process of the oven?
If your oven process involves:
- Turning a temperature dial to point towards a half-faded, hand-drawn chalk line
- Listening for a particular tone of “thump” or “hum” to know whether it has properly kicked on
- Or tapping your heels together to the beat of “Pinball Wizard”
… Then an oven upgrade can take the guesswork and crossed fingers out of your production and quality control processes. It will also improve employee onboarding while protecting you against future risks (like bad product runs and lost knowledge to employee retirement).
Non-standardized maintenance processes produce unnecessary operational costs. If your maintenance team shows up to fix an issue without understanding its cause, they waste valuable time on diagnosis. If they don’t have a repair process to work from, they spend even more time tinkering and triple-checking their work.
And when ovens aren’t maintained consistently, you run the risk of more frequent, more serious oven failures.
Most new ovens come with operation and maintenance guides. At Davron, we make sure to provide replacement part lists with all our equipment and can train your employees on oven operation and maintenance.
If your oven’s manufacturer no longer makes replacement parts for that model…
Then you risk lines going down over simple maintenance issues. Often there are aftermarket fixes and workable alternatives when it comes to replacement parts. But the more you rely on nonstandard replacements, the more variability you introduce to oven operation and maintenance.
And you put increased pressure on your maintenance and purchasing teams to stay ahead of potential problems when you complicate your replacement part ordering, especially if parts aren’t in consistent supply.
An oven upgrade can simplify your maintenance and procurement processes. Work with a dedicated partner you trust to support your operation for the long term, and you’ll avoid replacement part worries in the future.
Why an upgrade instead of a simple replacement?
Simply retiring your current equipment and replacing it with a near-identical model offers a simple solution to most of the issues above. But ovens are costly equipment meant to produce years of value for your facility. To swap in the new model without making a significant upgrade … that’s a wasted opportunity.
Upgrading off-the-shelf equipment to an oven tailored to your application and needs can reduce the risk of future performance issues and streamline all your operational processes.
Upgrading a batch oven to a conveyor oven can increase your efficiency hundredfold and unlock the opportunity for significant production capacity growth in your facility.
Upgrade to an equipment partner dedicated to understanding your application and supporting your operation now and in the future. You’ll count on customer service throughout the life of the oven.
Time for an upgrade? Ask for our help.
Davron’s custom process ensures you upgrade to a right-fit oven. We can tailor equipment to any process, application or specifications and talk through all the ways the right oven can upgrade your facility.
The perfect solution won’t appear on your doorstep overnight, and you may be surprised by the return your investment could generate quickly.
If you’re seeing any of the signs discussed above, don’t wait to reach out.