When is a custom industrial oven the answer for my manufacturing process?
Should your next oven be custom-designed, or would a more standard option suffice for your operation?
The question can be deceptively difficult to answer. And if you’ve posed it to the marketplace, you might have noticed providers’ funny habit of making it all about them and never about you.
So, let’s make this about you.
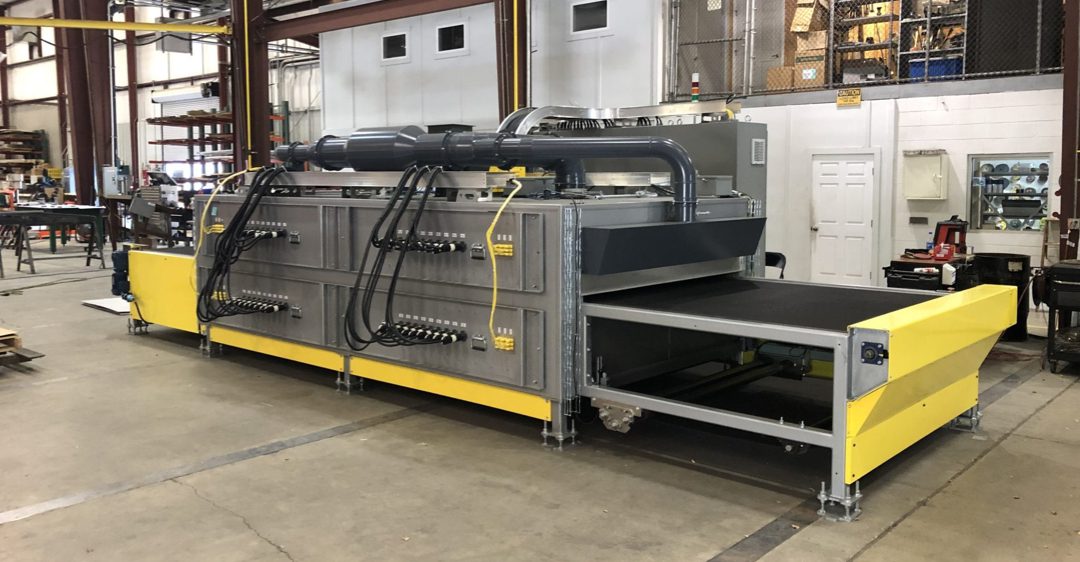
5 ways to consider if custom is right for you
The question of whether to bring a custom oven into your operation usually arises when something in your operation is changing, or when you’re reimagining a process to make it better.
While each of the circumstances below on their own would warrant considering a custom oven, in reality you’re probably confronted with a combination of them.
Workpiece geometry
The shape of your product will be a determining factor in this discussion in a few different ways.
For one thing, geometric complexity — including curves, severe angles or holes — introduces the risk that parts will warp or break under thermal load.
In some applications, this risk can be managed without changing thermal process parameters, but this isn’t always possible. When a more precise thermal process is the only option, consider a custom solution. A standard solution offering the degree of precision you need might not exist.
For another, regardless of your product’s thermal behavior, it simply might not fit inside standard machinery. Our work with an automotive industry supplier is the perfect example. The only way to process the injection molded interior components they manufacture was via a series of custom ovens:
- DTI-1423 indexing conveyor oven
- DTI-1302 overhead conveyor oven
- DTI-1255 overhead conveyor oven
- DTI-1200 overhead monorail conveyor oven
The right oven provider will understand how your product’s shape might impact the design of an oven. Davron engineers are highly skilled at applying unique product and process information to the custom systems they design.
Workpiece variety vs. volume
If you process a wide variety of product types, that’s a signal that a custom oven could be ideal for you. The key consideration here is volume.
If you have a wide range of parts and also process millions of each type, you’re probably better off buying a series of different ovens. But if you run a low enough volume of a wide enough variety, you’ll get the best bang for your buck investing in one custom oven that can handle all the work.
Here’s an example: DTI-1278 is a heat forming oven we designed for a honeycomb composites manufacturer. Product is loaded onto a cart that then rolls into the oven for processing. Due to the wide variety in the shape and size of parts, the cart is designed to accommodate different jigs and forms essential to various heat forming processes. The oven’s dimensions and airflow capabilities also are designed to assure performance across all product types.
Of course, custom ovens cost more up front. But remember that sticker price is only part of the story. You’ll reap rewards on the back end with just one oven to maintain.
On the other hand, if you find an oven off the shelf with the right dimensions, the right weight capacity, the right working temperature range and the ability to store and run multiple recipes, buy it.
Processing requirements and customer specifications
The complexity of a thermal process or strictness of your customers’ requirements also play a role in whether you need a custom industrial oven.
For one example, proper processing of a workpiece might require a very specific ramp rate and a soak temperature that cannot deviate a half a degree Fahrenheit in either direction for hours at a time.
For another, some processes require multiple zones of heating, with each zone precisely designed to achieve a specific result.
Such stringent requirements can be found in all manner of applications, but these are the ones we’ve seen most often:
- Thermal processing of safety-critical aerospace or automotive components
- Manufacturing of medical or pharmaceutical products, especially consumables or parts that interact with consumables
- Food processing
If the health and safety of people depends in any way on the performance of a part, its thermal processing requirements will likely be very strict — and that strictness will demand a custom solution.
Floor space limitations
Maybe your workpiece is simple and its specified thermal process is straightforward. But if a standard oven won’t fit on your floor, you’ve got a problem.
While this might seem like a silly reason to spend more for a custom solution, ask:
- Can I tolerate the downtime required to rearrange multiple pieces of equipment?
- Will that rearrangement cause a problem in my process or workflow that I won’t detect until it’s too late?
- If the only other solution is to expand my facility, will the bosses go for that?
- Are we willing to wait the duration of a construction project just to get this oven installed?
Maybe a custom-designed oven tailored to your space limitations isn’t such a wild idea after all. We’ve built many for our customers over the years, including this web-type foam manufacturing line.
It needed to be custom for a variety of reasons, but one of them was to preserve operator mobility despite its 200-foot length. A design feature allowed part of the system to raise up so operators could pass beneath it.
Think beyond your thermal process
Of course, heating constitutes but one part of a much larger process. A lot happens before and after thermal processing.
Our advice: Think holistically. You might recognize an opportunity to integrate custom material handling or other processing equipment upstream or downstream of your oven.
When these integrations are woven in ahead of and behind a custom oven, an even more efficient process that eliminates process variables is sure to result.
Learn what’s possible by reading about four real examples of pre- and post-processing equipment here.
Signs you don’t need a custom industrial oven
We love selling custom ovens, but obviously not everyone needs one. Custom doesn’t make sense when:
- You run only one thing through your oven and it is not shaped adventurously
- Your heating or airflow requirements are rudimentary
- Your customers’ specs are not especially onerous
Also, if you’ve read this much and your answer to the custom question is still “I don’t know” or “it doesn’t matter,” you probably don’t need a custom oven.
But if you want thermal processing equipment that perfectly matches your process and yields dependable, predictable results every cycle, then exploring a custom solution is the right call.
Is custom right for your process?
Maybe you already know what you need. In that case, we’re excited to see what you’ve got planned — upload your specs here.
But if you’re overhauling your process or beginning production of a new product, our engineers can help you determine the custom system that’s best for you.
Contact us to start the conversation.