Understanding industrial oven mass airflow
Mass airflow is an essential consideration in any thermal process relying on forced air.
Ensuring it’s even and balanced requires serious engineering grounded in a solid understanding of fluid dynamics.
Monitoring this information in real time is challenging, too.
Accurate mass airflow data is essential, but it’s only part of the equation. It must also be relevant.
These comingling complexities can catch manufacturers off guard, so we’re here to do some untangling.
As you’ll see, industrial engineers buying forced air thermal processing systems need a firm grip on a cascade of mass airflow considerations.
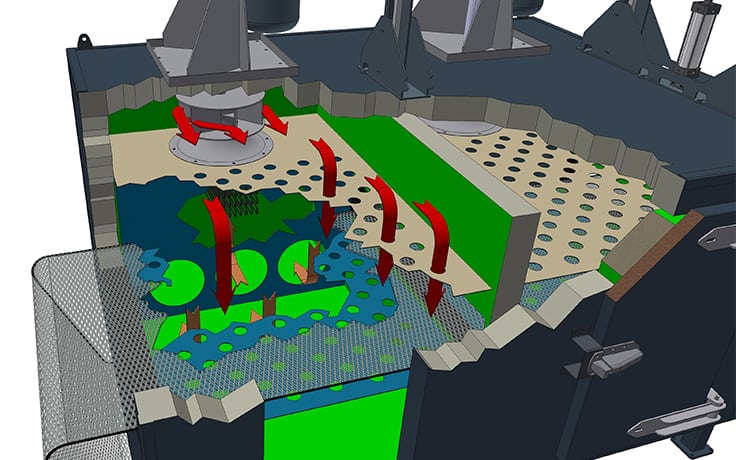
Why mass airflow matters
Because workpiece characteristics and process requirements can vary so widely, the way heat is delivered must be carefully considered.
We use the term “impingement” to refer to the impact forced air has on a product. That impact depends on the objective of your process, which will usually be one (or both) of the following:
Surface heating – Some processes require that the surface of a product be heated without impacting conditions in the core. Process parameters like temperature set point, fan speed, direction of airflow and soak time must be finely tuned to achieve appropriate product surface temperatures without impacting conditions in the core.
Core heating – Other processes require that heat penetrate through to the core of a product. The same process parameters apply and they must be just as finely tuned. If they’re not, a product core might reach its ideal temperature but its surface could be too hot. Or, if operators compensate for this phenomenon, the surface might be preserved but the core won’t be hot enough.
Regardless of the objective, heat must be delivered evenly. The impingement of hot air on a product must be uniform.
Uneven impingement will cause uneven temperatures across a part. Depending on the part’s makeup and the requirements of subsequent post-heating processes, some narrow temperature variation is tolerable. But in more sensitive applications, precise heating is a prerequisite for a part’s manufacturability.
Chronic uneven heating forces operators to choose between equally bad alternatives. One option is to run the process as-is anyway and hope their bosses can stomach the increased risk of waste or failed inspections. Or, they adjust processing parameters to compensate for the variability at the risk of incurring unforeseeable consequences or disrupting production cycle times.
(Read a real-world example of facility personnel confronting core and surface heating difficulties in this case study.)
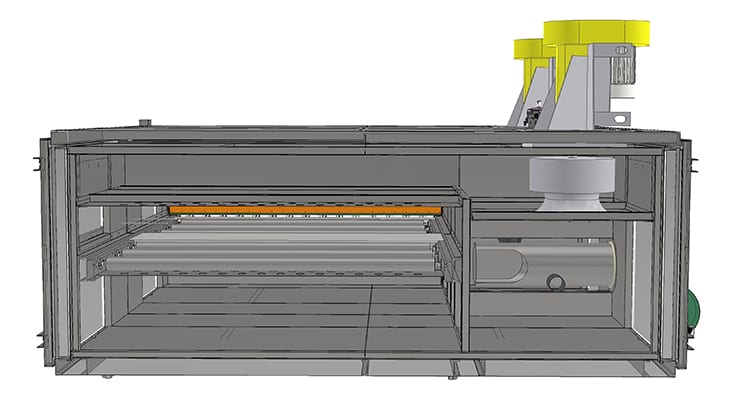
How mass airflow requirements impact industrial oven design
Above, we established why uneven air flow in an oven is problematic.
Things are about to get complicated, so it’ll help to understand the basic circulation pattern of air in a top-down, vertical-airflow oven:
- A powerful fan circulates air through the oven’s plenum system
- The fan pushes air through the supply plenum directly above the oven chamber.
- Air is forced through nozzles at the bottom of the supply plenum, moving downward toward the product.
- Depending on the product or process parameters, the heated air moves around or through the product in the chamber.
- After interacting with the product, the air is pulled into a return plenum at the bottom of the oven.
- From there, the air cycles back upward, past the heat source, through the fan and into the supply plenum again
Customer directives concerning oven system footprint often lead to the general compactness of plenum design. Combine this compactness and the effects of the laws of fluid dynamics and you’ve got challenges to address.
This is the complicated part.
Air will always take the path of least resistance. Picturing the same top-down vertical airflow oven as above, imagine air exiting a fan wheel then continuing horizontally at high velocity through the supply plenum. Most of that air will not naturally make the abrupt 90-degree turn after the fan to travel through a plenum opening and then into the product chamber. Instead, it will continue on the same horizontal path until it deadheads at the end of the plenum.
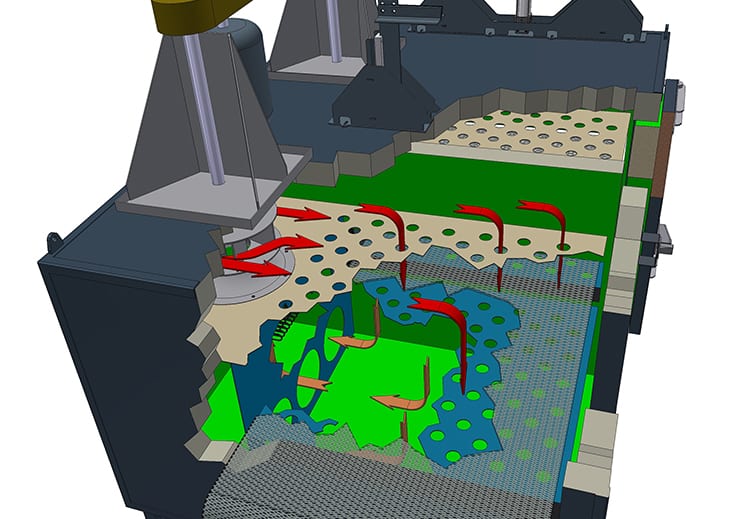
At this point the air has no alternative but to change directions. It will exit through the nearest plenum openings (those nearer the end of the plenum) and enter the product chamber.
But if the air prefers to exit nearer the end of the plenum, what about nearer the fan? Still sounds pretty uneven.
And indeed it would be — if the plenum nozzle openings all were the same area.
They’re not. The openings nearer the end are kept almost closed while those at the beginning are kept more open. By restricting the airflow at the end of the plenum, air—always taking the easy way out—also escapes from the supply end so that air volume enters the oven chamber evenly. The objective here is air volume uniformity at the nozzle, not uniform air velocity at the nozzle.
The short answer is this: Variable velocity owing to variable nozzle diameter does not impact the total mass of air moving from plenum to chamber. Velocity uniformity is achieved some distance after the plenum nozzles, after the air has diffused in the product chamber. Many process variables must be considered to determine the required distance from nozzle to product face, including:
- The weight and density of the product
- It’s permeability
- The product’s heating rate requirements
- Surface temperature vs. core temperature considerations
Industrial oven design impacts thermal process airflow monitoring
As you can see, mass airflow characteristics and plenum design matter a great deal to the success of any forced air thermal processing system.
As such, customers often want to keep an eye on these variables.
But, here’s an important note. A product’s heating profile is the ultimate determinant of how well airflow is balanced. Mass airflow monitoring techniques provide operators sources of data they can use to fine-tune their operations. A word of caution: There are many ways to monitor this, but they’re not all relevant.
Velocity is a typical example. It’s common to see specifications for velocity sensors at plenum nozzles to verify that the volume of air entering the chamber is even. The assumption is that if each sensor records the same velocity, airflow into the chamber is balanced.
But as we noted above, plenum nozzle openings are designed to varying areas as the first step to compensating for pressure differentials inside the plenum. Measuring velocity across a series of nozzles would only be meaningful if the plenum system was designed to achieve uniform mass airflow and uniform velocity. Davron can and has designed specialty plenum systems that provide uniform mass airflow and velocity simultaneously, but applications requiring such complex and more costly plenum systems are rare.
So, what alternative measurement do we recommend?
A piezometer ring.
These instruments are used in all sorts of applications but you might recognize another form of these instruments—pitot tubes—as integral aircraft components.
In the case of mass airflow monitoring, we specify piezometer rings in the narrowest section of the inlet cone of the circulation fan to measure vacuum at the inlet. We compare that to the vacuum inside the return plenum to determine the pressure differential between those two points.
Those numbers are crunched in the system’s PLC to provide an accurate, relevant mass airflow reading in real time. This is crucial: Air pressure and temperature are directly related, so as one changes, so does the other.
Balancing the system is like shooting at a moving target second by second. Depending on the complexity of the system, airflow parameters can be adjusted manually or automatically to stabilize mass airflow.
Real-time data must be accurate AND relevant
You can see what we meant when we said “cascade.”
Mass airflow characteristics matter a great deal in forced air heating applications.
The process requirements within those applications drive key aspects of industrial oven design.
Industrial oven design characteristics determine the relevance or irrelevance of available mass airflow monitoring methods.
If your manufacturing operation includes forced air heating, even mass airflow is going to matter. The way it’s monitored must be accurate and relevant, and that’s where an experienced industrial oven provider can assist.
Have a project coming up? Have questions about how to ensure mass airflow in your industrial oven system is balanced? Need a hand in determining the most relevant metrics to include in your specifications?