Case study: Pre- and post-processing add-ons streamline manufacturing
Thermal processing plays an essential role in countless industrial and manufacturing processes.
Accordingly, the knowledge and skill that an industrial oven manufacturer brings to the table is obviously important. But how far beyond a thermal process should equipment providers be able to see? How well must they understand the stages that come before and after the thermal process?
In our view, they should be able to see all of it.
We champion a whole-system approach, building not only ovens but the pre- and post-processing equipment that complements them.
Let’s start by summarizing the concept and its compelling benefits.
Then, we’ll describe four projects in which Davron’s pre- and post-processing equipment expertise helped customers across the industrial spectrum realize more seamless, more reliable operations.
Pre- and post-processing add-ons drive operational & cost benefits
Most manufacturing lines feature a series of individual machines made by different providers.
This standard practice subjects each machine to the specs and potential limitations of its neighbors, which were designed, built and programmed by disparate teams. Facility engineers are on the hook to overcome the barriers that pop up at every transition from machine to machine.
What if you weren’t on the hook for that? And what if those barriers vanished? Consider the holistic advantages of engaging just one provider for industrial ovens plus any required pre- or post-processing machinery:
#1 – Engineers can identify opportunities to specify the same parts across different machinery when it makes sense, simplifying maintenance and spare parts sourcing
#2 – Similarly, a whole-system approach allows for more seamless electrical engineering that makes panels and wiring easier to understand and maintain
#3 – No costly automation software integrations are needed when industrial ovens and adjacent handling or processing operations are engineered as a single system
#4 – Because single-source systems come with only one operator/maintenance manual, your team will never have to ask if they’re looking at the right resource
#5 – Whole systems allow for unified operator safety features and procedures and eliminate the need to make costly aftermarket tweaks
#6 – Line operations are less impacted by floor plan restrictions or user flow requirements when processing and material handling stages are engineered together
If you want to dig deeper into the benefits summarized above, read about the cost benefits and operational benefits of single-source whole-system manufacturing.
The articles specifically cover foam manufacturing lines but can apply to any industry we serve.
Four game-changing systems utilizing pre- and post-processing machinery
Foam expanding oven & conversion – In this case, a global foam manufacturing firm ordered a 60’ continuous conveyor oven to expand webs of cross-linked polyethylene foam. Our initial work was confined to building the oven, which featured six zones of temperature control and variable speed capabilities. Post-processing equipment was sourced from a variety of other vendors.
A short time later, the customer expanded its capacity and we processed an order for another 60’ oven. But this time, they asked us to incorporate the oven into a larger system that would process and prepare the foam webs for shipment. Five additional machines constitute the foam conversion equipment we tacked on to the end of that second oven.
Foam manufacturers keep their cards close to the vest, so it’s hard to know how well the system works. Well enough, evidently: This customer has since added two additional complete lines to its facility.
Constant-tension foam cutting and winding – As noted above, manufacturers can level up their operations regardless of space constraints or user flow limitations if equipment providers can engineer whole systems.
That was the case with this custom processing equipment we built for a global foam manufacturer.
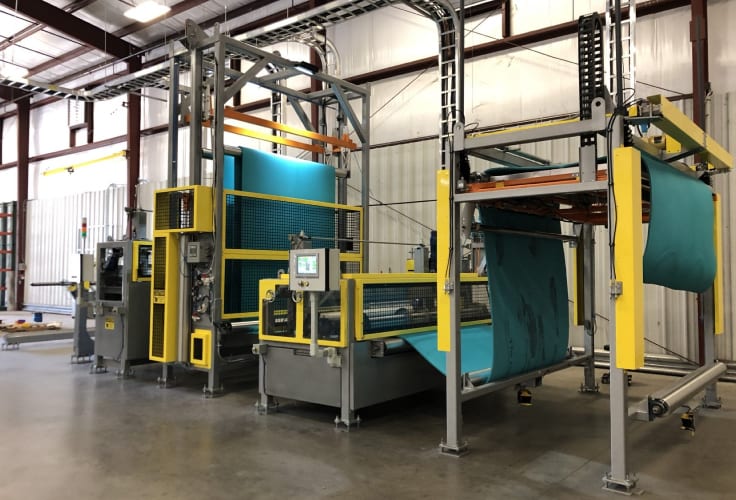
The equipment can process foam webs from 36 to 96 inches wide at up to 40 feet per minute. It can cut whole webs down to as many as 10 strands and features some one-of-a-kind design innovations we developed to meet the customer’s unique requirements.
Read more about this unique system (and watch video footage from a test run) in this case study.
Contact + IR oven and processing – Installed within an automotive textile manufacturing line, this system draws a carpet layer and a backing layer from separate rolls onto separate conveyors. Then, an auto-alignment system ensures the layers are perfectly aligned. This alignment is critical later in the process.
Once the layers are oriented properly, indexing conveyors move the layers into the oven chamber for heating. After heating, the layers are stacked one atop the other and a shuttling conveyor moves them into the press tooling where they’re formed.
The design for this system is a departure from the norm. Most often, systems like these receive pre-cut blanks instead of drawing material from rolls. But in this case, the customer’s project requirements were such that this uncommon design — which churns out a vehicle set every minute or less — made more sense.
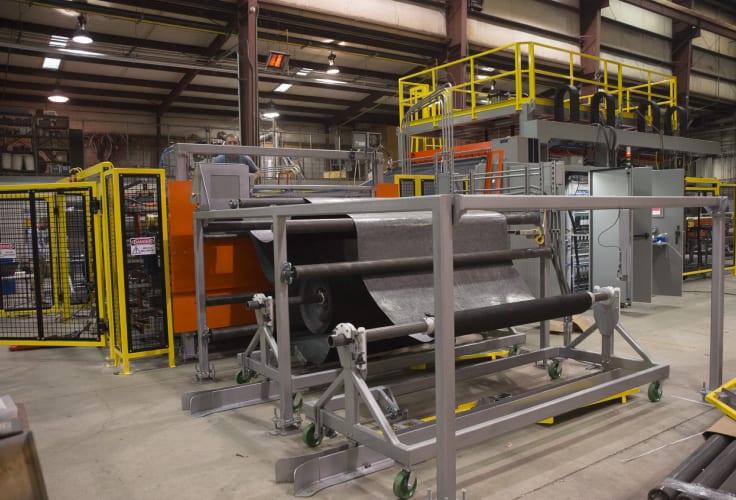
Indexing annealing furnace system – The customer in this case was a major global automotive component supplier. Proper annealing of the metal parts they make in their facility required processing in a 99.8% inert environment.
A unique challenge in this project was the “one-in, one out” nature of manufacturing in this facility. Parts were processed one at a time at every stage except during annealing. This was done in batches, creating a clumsy bottleneck in production.
The index annealing furnace system we delivered was uniquely complex. Parts are placed one at a time on a shuttle table at the entrance of the system’s purge vestibule. Each part then travels into the vestibule for the nitrogen purge.
From there, a pick-and-place robot moves the parts to a tray, and trays cycle through two heating sections. After the heating, the batches move through a forced-air cooling stage. Upon cooling, another pick-and-place robot retrieves the parts and places them on a shuttle table in a rear vestibule. This all occurs in an oxygen-free blended atmosphere.
Finally, a third robot retrieves the parts one by one to resume the facility’s precise cadence.
The system is timed to match the per-part cycle time of 45 seconds in the facility. The old inefficient batch system is gone; its replacement has resulted in a much more consistent process. We’ve since delivered three additional identical annealing systems to this customer.
Can it work for you?
The project summaries above show that adding pre- and post-processing equipment to an industrial oven can simplify processes, eliminate inefficiencies and improve quality and consistency.
To learn if a more holistic system makes sense in your facility, ask these fundamental questions:
- Do the machines in your lines work well together, or do they often fall out of sync?
- How many operating manuals do your process engineers consult when they’re troubleshooting?
- Are they stuck figuring out which vendor is responsible when problems occur in the transition from one provider’s machine to another’s?
- How many different vendors’ phone numbers do they have on speed dial?
- Is programming and installation of new equipment more like a symphony performance or a wrestling match?
- How many HMIs do your operators need to know how to navigate?
- Are you confident in the safety of your piecemeal manufacturing lines?
What’s working in your facility? What’s not working? What would you like to see change? Contact us to talk it over.