Structural steel walls vs. tongue and groove panel walls
If there were an Amazon.com of industrial ovens, where you could scroll through pages and pages of industrial ovens of varying value to your operation, you would notice something: They would almost all have the same type of oven walls.
Tongue and groove panels with vertical seams, up and down pages upon pages of results. And there’s a reason for this.
(Hint: the reason is cost).
But we choose to build ovens that outperform the industry standard, for manufacturers who need a higher level of performance from thermal processing equipment.
This article breaks down the drawbacks of panel ovens, what makes a Davron oven different and the reasons behind each oven-building approach.
The problem with tongue and groove panel oven walls
Most industrial ovens on the market utilize walls built from tongue and groove panels. Metal panels use tongue and groove joinery to stand flush against each other, and then they’re bolted together from the outside in.
Well-designed panel ovens account for thermal expansion by using grooves that are longer than the corresponding tongues. This reduces oven warping over time.
The primary performance drawback of a tongue and groove panel oven relates to how they’re bolted together. Since each bolt runs through the plane of the panel wall, it has an end inside and outside the oven.
Here’s the problem: The more metal you have from the oven chamber to the oven exterior, the more heat loss and heat transfer you have in your oven system.
This affects your oven’s ability to maintain consistent uniform temperature and produce a consistent product. When that happens, scrap rates go up and maintenance halts production more frequently.
And on a large oven, that amount of heat transfer makes a difference in terms of wasted energy.
An often overlooked drawback of tongue and groove panel ovens?
Their burdensome installation.
This is an especially serious problem for large ovens. Small ovens can arrive at your facility fully assembled in most cases, but large industrial ovens likely won’t fit on trucks or through plant doors.
And the amount of labor required to assemble a panel oven scales unfavorably with the oven’s size. Some large ovens require assembly in your plant of over 50 panels.
That’s a lot of joints, and a lot of assembly taking place on your manufacturing floor. Panel walls are a big reason why some shop-floor oven installations hold up production for months.
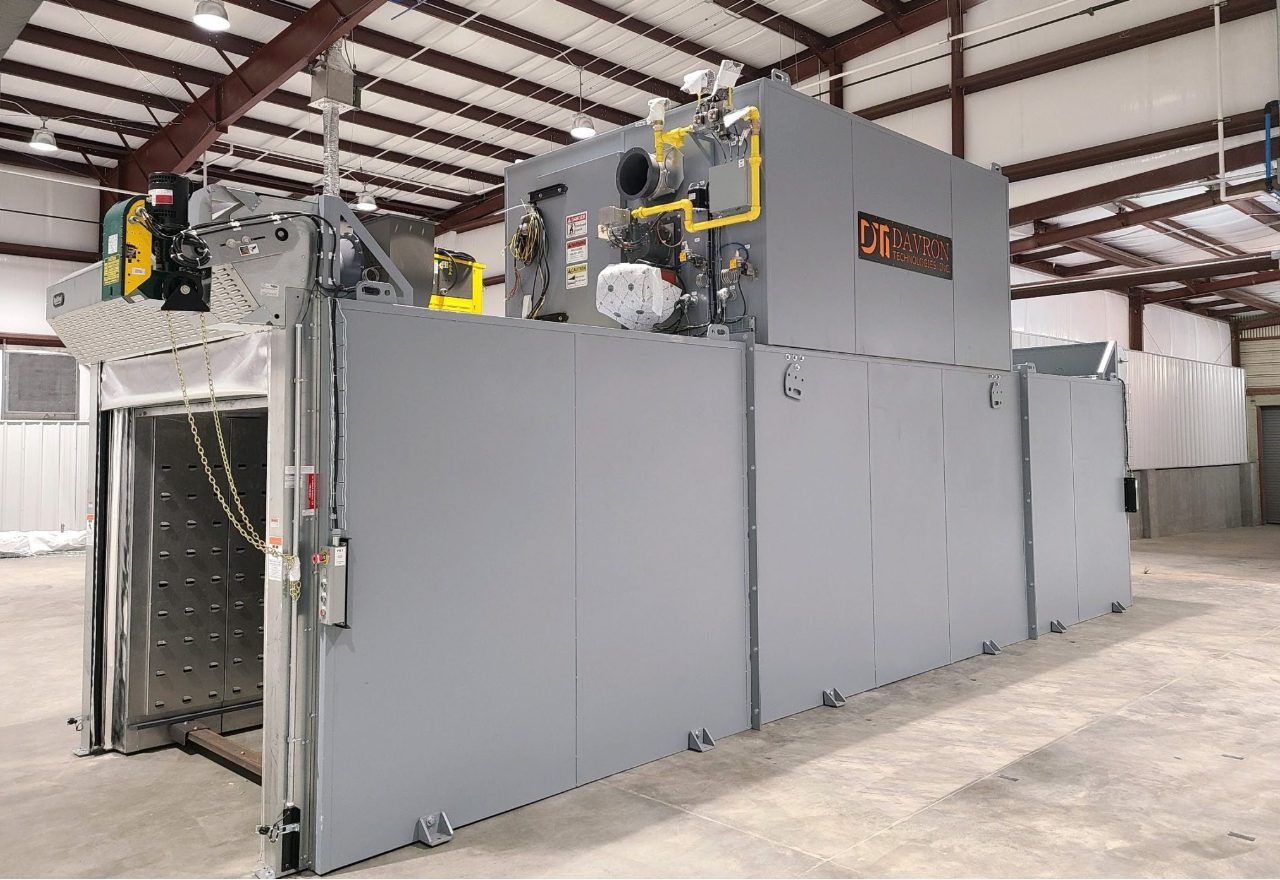
Structural steel oven walls for better performance
Davron builds ovens with structural steel walls instead of tongue and groove panels. Large steel modules are sealed together with a gasket system. To maintain the complete seal of the gasket system, angles on the ends of the modules are attached together by companion flanges on the oven’s exterior.
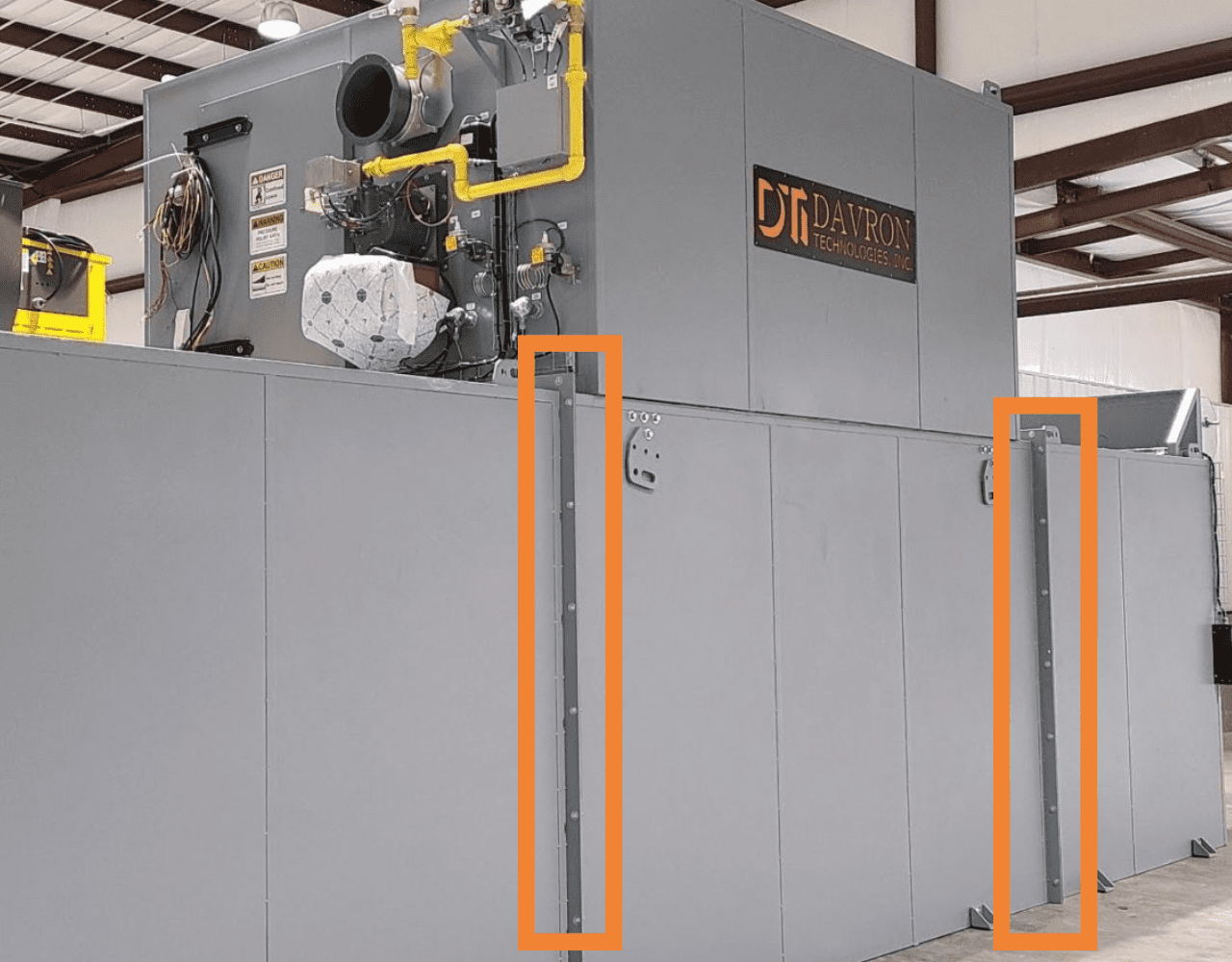
From a view of the inside, you can see the plenum wall with vertical expansion joints that run the height of the oven interior. Behind the plenum wall is the interior oven wall, which has all the same expansion joints in the same places of each module, up the walls of the oven and on the ceiling.
There are two main advantages to building ovens this way:
- Your oven maintains proper temperature more reliably and requires less energy to run. This is because it has absolute isolation from inside wall to outside wall to minimize unwanted heat transfer.
- Your oven maintains its structural integrity indefinitely, with no risk of warping. When the oven heats up, it can expand and contract in alignment, like an accordion.
Simple installation of a structurally robust oven
Since Davron ovens are built and assembled in large modules, installation becomes much simpler.
The 35-foot oven shown above makes for a good example. It was built in four modules and fully assembled in Davron’s facility for final testing.
When we broke the oven back down into four separate modules (to fit it onto trucks and through the customer’s plant doors), key parts like fans and motors remained bolted to the top module. Installation of the entire oven in the customer’s facility and a successful first runoff took less than a week.
Why we build a different oven
It would be easy for us to say, “We build ovens this way because they’re the best, and we’re the best, full stop.”
But we’d be ignoring the fact that, for us, there’s a compelling business case for producing ovens with structural steel walls. And for most other oven manufacturers, there’s a compelling business case for producing panel-walled ovens.
Why most ovens use panel walls
Most of the biggest oven manufacturers in the U.S. maintain a catalog of oven templates. They’ll build any oven within those templates. Some will “customize” ovens by starting with one of those templates and modifying certain elements.
Because they sell templated ovens, they’re able to develop economies of scale by using like panels across a variety of different ovens. 12-by-8-foot oven? That’s four 3-by-8-foot panels. Need a 15-foot long oven? That’s just one more of the same panels on each side.
Some oven manufacturers have their own panel production lines in their facilities. Others contract panel manufacturing out to a third party. Either way, it delivers value to their customers in terms of affordability. So there is a good reason panel ovens exist.
Why we build ovens with structural steel walls
Since we build entirely custom ovens — based on your needs, not from templates — we wouldn’t achieve any meaningful economies of scale by using a panel wall system for oven production. So there’s no temptation to short-change the integrity of our oven walls for the sake of cutting cost.
In working with hundreds of manufacturers on designing the exact oven that their facility needs, we’ve never come across an application that would benefit from tongue and groove panel walls. And we’re right there in CAD, able to design a structural steel system as simply as we could any other.
We don’t design one-of-a-kind ovens to offer affordability to folks with simple thermal processing needs. We do it to offer better oven performance and a unique process fit to manufacturers who have unique thermal processing needs.
Where’s the ROI? Our customers see it in:
- Longer service life
- Better temperature stability
- More precise and consistent heat delivery
- Ultimately, the ability to deliver better products to their customers.
Ready to upgrade to a best-in-class industrial oven?
Structural steel walls are only one benefit among many that come with an oven tailored around your thermal processing needs. If standard thermal equipment slows down your production or causes process headaches in your facility, get in touch with us.
We can design and build an oven to meet a challenging set of specifications or start with pre-engineering to collaborate on a quote-ready oven design.