Batch vs. continuous ovens: What’s right for your facility?
How to know which oven type suits your process needs
When specifying thermal processing equipment, you need to make choices based on your unique production process and facility capabilities. Do you need a gas or electric oven? Convection heat or infrared? The product you process, the materials that compose it and your facility’s capabilities all combine to drive these important decisions.
A common question you’ll need to answer: Should you use a batch oven or continuous oven?
Each has its place, so there is no universal “right” answer.
More like, “It depends.”
Put as simply as possible: If you process low volumes of unique parts, then a batch oven is ideal. In almost every other case, a continuous oven will provide more value.
Batch ovens
The first thing that sets batch ovens apart for many manufacturers is the sticker price. Often, they’re significantly cheaper than continuous ovens. This comes with caveats, though, like the need for more involved human operation and dramatically reduced throughput compared to continuous ovens.
Batch ovens are perfect for applications where part sizes, shapes and materials vary significantly. The powder coating industry loves batch ovens for this reason. Say you’ve got a powder coating contract with an automotive exterior manufacturer. One day you’re processing door handles, the next day it’s bumpers. A batch oven derives versatility from its simplicity — when the only equipment variables are temperature and time, setting the oven up for a different run is easy.
There are also applications for which putting a part on a conveyor and blowing hot air on it may not be viable, like in pharmaceutical production. If you’re processing powder for pills, you’ll want to make sure the powder stays in its tray and rests uniformly. Running that tray on a conveyor could introduce quality control issues that a batch process would alleviate.
That said, it’s important to know what capabilities you need from your batch oven. If you need something cheap and easy, consider an off -the-shelf oven. We understand that some industrial processes just don’t have sensitive requirements.
But batch ovens (like our customers’ processes) aren’t always simple. If you’re looking for an oven with exceptional temperature control or the ability to meet unique parameters with clockwork consistency, then you’re our favorite kind of manufacturer.
Maybe you need an oven that can switch between processes quickly to cut your downtime. Maybe you need something big enough to anneal industrial storage tanks. Maybe your thermal process needs an inert atmosphere. A batch oven may offer the simplest tool for achieving a difficult result. And working with Davron on an oven custom-made to your process ensures your thermal process is best-in-class.
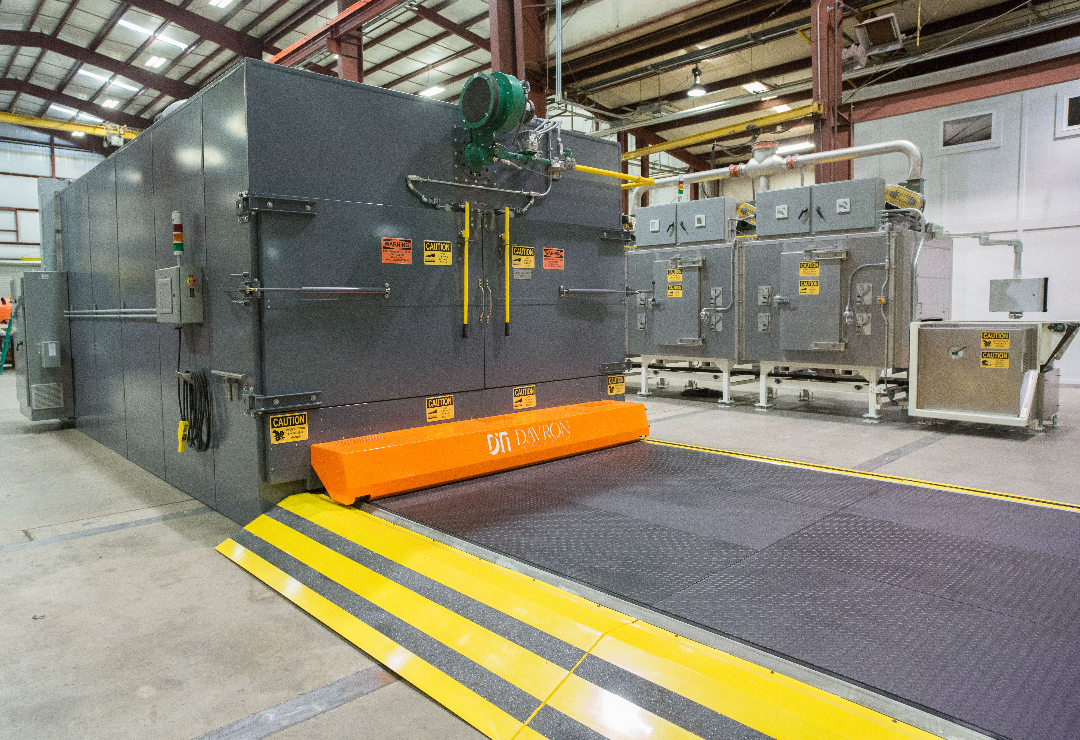
The drawbacks of batch ovens
Batch ovens aren’t perfect for every application and have their fair share of drawbacks.
When batches contain multiple identical parts, how they’re arranged in the oven can affect how they respond to thermal processing. This makes consistent heating of every part challenging. Parts set near the oven’s perimeter will reach the target temperature first, then “soak” longer as the parts in the middle heat up. This risk of overheating perimeter parts can make product quality inconsistent.
When a thermal process requires cooling in addition to heating, batch ovens require a much longer cycle time because the same chamber that just heated up now needs to cool down again. Then it will need to heat up again, cool down again, ad infinitum. In these scenarios, continuous ovens can move parts from a heating chamber to a distinct cooling chamber to dramatically reduce cycle time and save on energy usage.
Batch ovens require labor and time to load and unload. When processing endlessly variable parts at low volumes, this may be necessary. But for high-volume production of identical parts, a more automated system that minimizes operator intervention is ideal.
Continuous ovens
Unless you’re processing highly variable parts at low volumes, a batch oven is probably wrong for your operation. But a continuous oven likely offers the perfect set of capabilities for your needs.
Because the product moves through the oven identically to every other part, each part receives the designed amount of heat. If you’re using air to heat a part, you’ll achieve more even heat impingement with a continuous oven using a conveyor than you would with a batch oven.
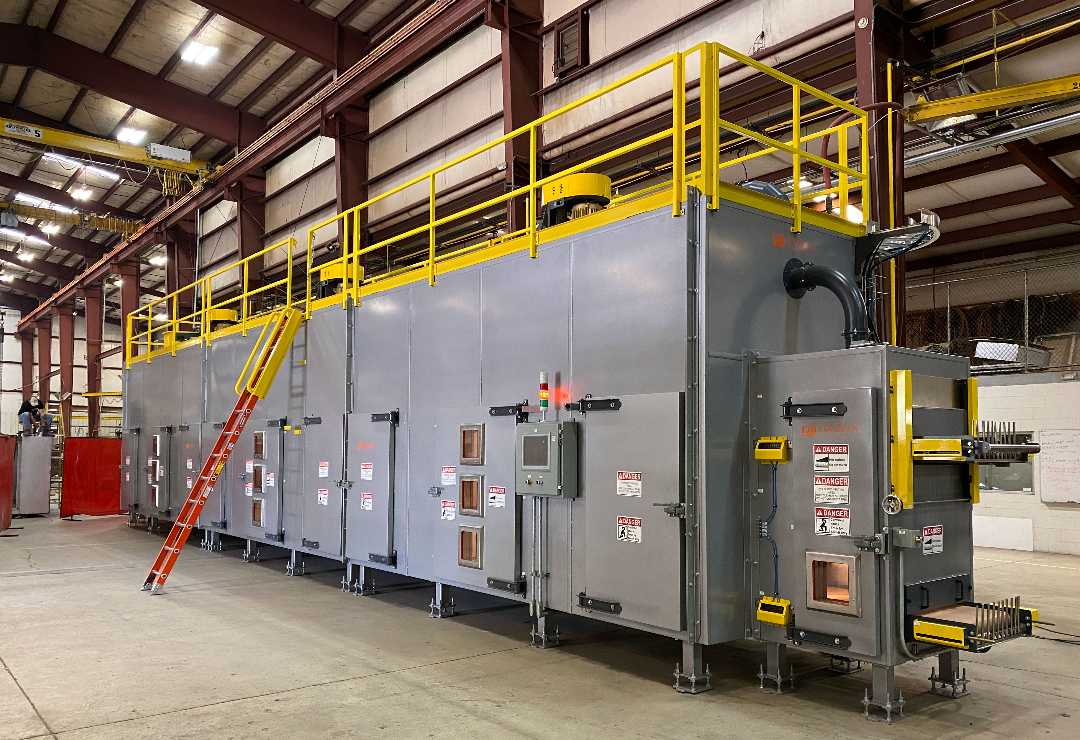
Continuous ovens can also be engineered to include variable temperature zones to perform multiple parts of a complicated thermal process within a single machine.
When a manufacturer needs to cool parts after heating them, the continuous oven simply moves the parts from a heating zone to a cooling zone. In this way, a continuous oven can turn a complicated process into an efficient one. Maybe a part needs to be pre-heated gradually or brought to a reasonable temperature before annealing. Or maybe a part needs to be cooled gradually after curing. A continuous oven can make use of multiple heating zones for any processes that may shock their parts with extreme temperature changes.
Variable temperature zones deliver safe preheating of automotive carpets coming in from the cold
Read the case studyContinuous ovens run constantly, accepting new parts for processing via some type of conveyor, with little need for human intervention. In terms of the details of the conveying, type of heating (convection, infrared, etc.), size, goal temperature and cycle time, just about anything is possible and technology pushes forward constantly.
An example to illustrate the impact of a continuous oven
Say it takes one minute to load six identical parts into your batch oven and one minute to unload them. And your processing time is five and a half minutes, including time for the oven to cool down. That means six parts are processed in seven minutes and thirty seconds.
A continuous oven processes parts constantly. Parts can enter and exit the oven at any throughput, provided you have space in your facility.
Those same six parts as above could enter a conveyor oven one at a time every ten seconds and exit at the same rate. One minute to load six parts and one minute to unload, just as before. Let’s assume the same processing time to show the impact a process-oriented change can have.
What’s the difference? Your hypothetical batch oven only processed those six parts in the given timeframe. But a continuous oven is constantly accepting new parts. If you do the math, the hypothetical continuous oven (with identical processing time and loading/unloading time) worked on a total of 45 parts during that same timeframe. A completed part will exit the oven every ten seconds, no labor required.
Other than the occasional scheduled maintenance break, the continuous oven can process a part every ten seconds for the next ten years (probably even longer). Assuming 24 hours of maintenance time per year and continuous operation through holidays (without accounting for leap years), that’s 31,449,600 parts processed during the life of the continuous oven.
Assuming no maintenance whatsoever (impossible) and continuous operation through holidays, a batch oven with the same cycle time would process only 4,204,800 parts (over 27 million less), while costing you ten years of additional labor expense.
What could those operators do for your company to add value over ten years? Probably a lot.
Addressing hesitancy about continuous ovens
So why isn’t every volume manufacturer using a continuous oven for thermal processing? The two biggest reasons are resistance to change and up-front cost.
Manufacturers don’t like fixing what ain’t broken. And why should they? When you’ve used batch ovens for 40 years, it can be challenging to ditch something that you know works. Especially when it’s costly.
We encounter a lot of skepticism regarding whether a continuous oven can perform adequately based on the uniqueness of a manufacturer’s application. In truth, continuous ovens can meet all the same thermodynamic criteria that batch ovens can. Plus, they’re designed to heat and cool every product identically for the most consistent processing possible.
Do some applications produce design challenges? Sure. But we haven’t seen anything that creative thinking and experienced engineering couldn’t solve. Whether you need particular airflow or an operating temperature of 1600°F in a 99.8% inert atmosphere (see: indexing furnace with automated airlock), we can design around any criteria.
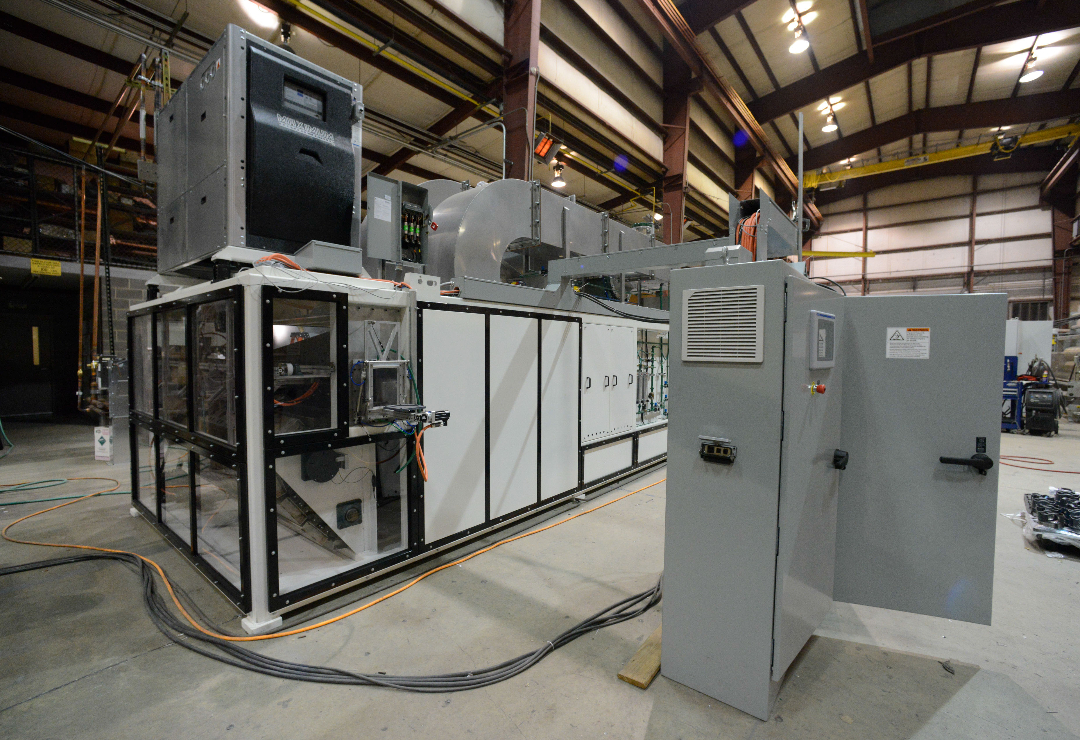
In terms of the high up-front cost of a continuous oven, it’s clear that the lifetime value of a right-fit continuous oven outpaces that of a batch oven by light-years. Using the above example and assuming your parts are sold with only a $1 margin, the continuous oven would be worth at least $27 million more than the competing batch oven, while costing a fraction of that value.
If you know what production rate you’d need for one year’s payback on your purchase, a continuous oven can be designed to make that rate.
Time for a new oven? Think custom.
When it comes to choosing between a batch and continuous oven, the decision could change the trajectory of your company. Whether you know what you need or are looking for a more detailed conversation about your application, talking with an engineer is a great place to start.
Work with a custom oven manufacturer and determine the best possible oven for your facility, down to the details. How could a different conveying system into the oven make your process more efficient? What value could your oven operator provide elsewhere in your facility if the oven ran itself? Could your batch oven alternate between modes five times faster?
We can help answer those questions. Send us rough specs to get started.