Aerospace composite thermal processing 101
One thing that OEMs, militaries and garage tinkerers have had in common since the dawn of aviation is an obsession over building aircraft that are lighter and less costly to fly.
That pursuit is manifested today in the composite honeycomb material used in the production of components ranging from simple flooring panels to complex, safety-critical segments of wings, tails and bodies. Indeed, some modern aircraft are made of 50% composite materials by weight. That ratio will only increase.
Thermal processing of these materials is one of the most important manufacturing stages. Done well, the result is a marvel of aerospace engineering that industry stakeholders know is essential to continued innovation in aircraft design.
But if it’s done poorly, aircraft may experience an unplanned event miles above the ground.
And while the onus is on OEMs and their suppliers to verify airworthiness, oven manufacturers nonetheless play an instrumental role of their own.
It’s not for beginners.
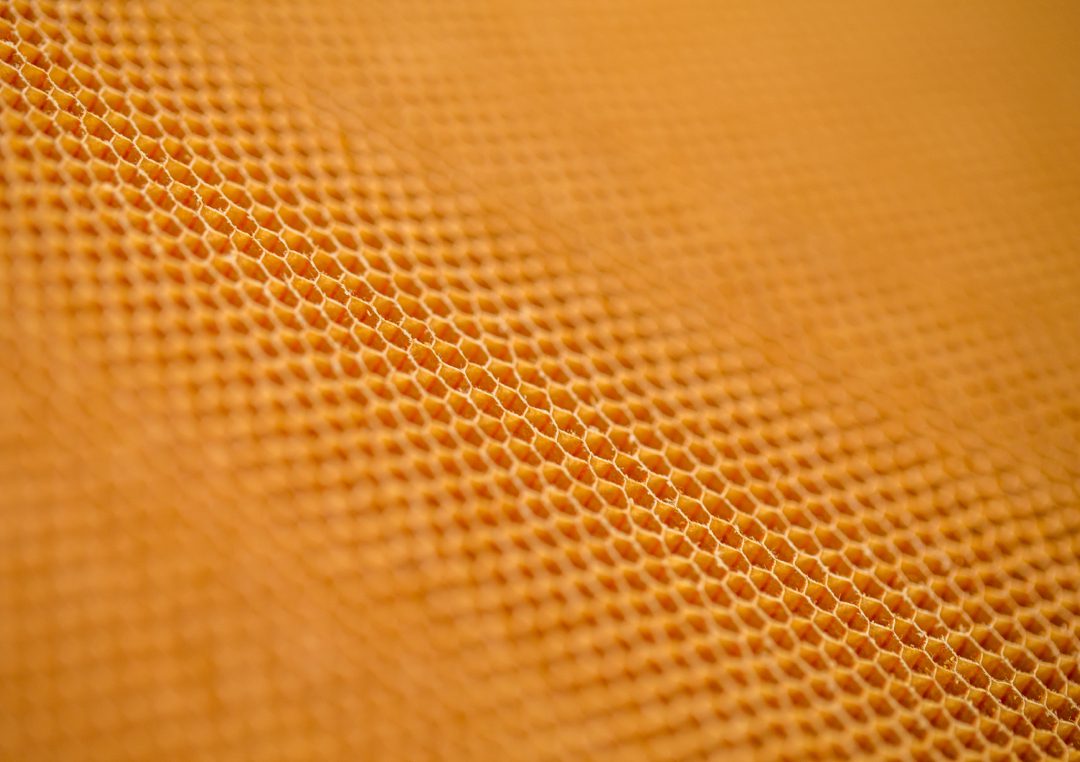
Material specs will drive curing oven design and cost
Thermal processing for aerospace composites mainly comprises the drying and curing of “blocks” of fibers coated in either solvent- or water-based resin.
The specified resin is the primary driver of curing oven design as well as some of the thermal processing parameters. Consider this brief comparison of thermal processing using water- or solvent-based resins:
Resin type: Water-based
Approximate cycle temperature: 350 – 400 degrees Fahrenheit
Approximate cycle time: Up to 16 hours
Makeup air requirements: Moderate
Resin type: Solvent-based
Approximate cycle temperature: 350 – 400 degrees Fahrenheit
Approximate cycle time: Three to four hours
Makeup air requirements: Significant
Curing honeycomb material coated in water-based resins takes much longer because water evaporates more slowly than other solvents. But what manufacturers may feel is lost in an overlong cycle time they gain in an oven that is comparatively simpler to engineer, cheaper to build and much safer to operate.
For example, curing water-based resin creates much less volatile byproducts that must be exhausted. Because process cycles require far less makeup air, the makeup air intake systems don’t need to be as complex.
For another, these oven types do not require the same degree of explosion prevention, again due to the relatively low load of volatiles released as a byproduct of curing.
Solvent-based resins cure in a fraction of the time it takes to cure water-based resins. But the process results in the release of a much higher volume of volatile compounds and is therefore far more dangerous.
In these ovens, both the exhaust and makeup air requirements are significantly enhanced. Engineers must also appropriately size the ovens and their inner air distribution components so that at no point can the system reach a vapor concentration conducive to explosions.
Additionally, oven air supply design must account for exothermic conditions in cases where the specified resin will result in a chemical reaction as it cures.
Other fail-safes include:
- Redundant solvent monitors and temperature sensors throughout the system
- Automatic heat source isolation and “flooding” of clean air if an unsafe condition occurs
- Explosion relief panels that channel explosive energy upward instead of outward for operator protection
- External thermal oxidizer systems that destroy volatile byproducts
These added engineering requirements and fail-safes make ovens that cure solvent-based resins relatively safer to operate but more complex and expensive to build, particularly in the case of thermal oxidation.
But within that expense is an opportunity: Thermal oxidation of volatiles creates a lot of heat. With the addition of a heat exchanger in the system, that heat energy can be harnessed and directed back into the process.
This reduces the reliance on a primary heat source, enhances the efficiency of the process and contributes to more sustainable operations.
A note on heat source
In almost every circumstance — whether you’re processing a water-based or solvent-based resin — the heat will come from natural gas burners.
It’s the most economic source by far; composite curing and drying requires an amount of heat energy that would make electric heating prohibitively expensive.
Pre- and post-heating process control considerations
Obviously, thermal processes like curing and drying must be repeatable and precise to ensure honeycomb materials will perform as intended.
But other aspects of aerospace composite manufacturing must be just as precise, so the upstream and downstream equipment responsible for these processes must also be designed with care.
One of these aspects is the way that virgin blocks are repeatedly dipped in resin. For best performance, blocks must be evenly coated, a process requiring careful calibration. Once plunged into dip tanks, blocks must be lifted at a varying rate.
If a dip system cannot achieve the specified precision reliably every cycle, there would be no way to verify even coverage and the risks of delays or wasted product are amplified.
Another aspect is the condition of the resin itself. Ensuring the correct resin viscosity is key. No amount of tweaks to the dipping, curing or drying processes can compensate for resin viscosity that’s out of spec in either direction.
It’s essential that manufacturers are aware of — and prepared to respond to — conditions that can impact resin viscosity. Those include ambient facility temperatures (daytime-nighttime fluctuations as well as seasonal fluctuations) and the temperature of components that deliver resin to dip tanks, such as pumps, filters and piping.
While ovens are Davron’s bread and butter in the aerospace sector, we’ve also developed expertise in the design and manufacture of resin dip tank systems. Design features can include:
- Temperature-controlled bulk storage tanks
- Mixing systems inside tanks that help maintain viscosity and temperature throughout
- Viscosity meters to show operators whether thickening or thinning agents must be added based on resin conditions
See examples of custom dip tanks we’ve built here and here.
We’ve also engineered custom aerospace composite block presses which are instrumental in guaranteeing blocks meet dimensional requirements prior to cutting or machining.
Custom equipment for complex products
As aerospace innovators continue the search for more perfect materials, equipment providers must be prepared to match the effort by designing machinery that pushes the envelope.
At Davron, everything we build is custom-designed to meet customers’ rigorous requirements. And aerospace is as rigorous as it gets.
If you’re considering adding, modifying or replacing honeycomb material processing capacity in your facility, our engineers would love to learn more about your plans. Get in touch with one here.